I. Introduction to BX Wavelength Dispersion X Fluorescence Analyzer BX Series Wavelength Dispersion X Fluorescence Analyzer is the foundation of Beijing Bangxin Weiye Technology Development Co., Ltd. on the basis of the national “9th Five-Year Plan†research project, summarizing the development of X fluorescence analyzers in China for many years. Based on the experience and lessons learned, and absorbing international advanced technology, it has in-depth research and development of industrialized high-tech products. All technical performance indicators have reached the international advanced level of similar products.
As a routine analysis method, X-ray fluorescence spectrometry technology began in the 1950s; after more than 50 years of development, it has become one of the essential methods for material composition analysis. With the continuous development and progress of analytical methods and related technologies (especially computer technology and electronic technology), X-ray fluorescence spectrometry has not only become an important analytical tool in the fields of geology, metallurgy, petrochemicals, semiconductor industry, and medicine and health, but also A fast, accurate, and economical multi-element analysis method commonly used in materials science, life science, environmental science, etc.; especially in the field of industrial conventional component analysis, X-ray fluorescence spectrometer is internationally recognized as the dominant analytical instrument. , Widely used in iron and steel, metallurgy, building materials, petrochemicals, mining and other materials industries; At the same time, X-ray fluorescence spectrometer is the field instrument analysis and process control analysis and other aspects of the preferred instrument.
For a long time, wavelength-dispersive X-ray fluorescence analyzers that are suitable for use in cement production enterprises have all depended on imports; expensive purchase costs, spare parts costs, maintenance and repair and technical service fees have made China's cement manufacturers overwhelmed; at the same time, more than 8 weeks have passed. The spare parts delivery cycle has had a serious impact on the normal production of the cement plant.
The successful development of the BX Series wavelength dispersion X fluorescence analyzer completely broke the monopoly of this technology by foreign instrument companies and provided a high-performance, cost-effective process control solution for the majority of domestic cement production enterprises. And technical services are better than imported instruments, and the related costs are much lower than imported instruments.
II. Project content and purpose and significance of project implementation NSP cement production technology is based on levitation preheating and pre-decomposition technology, and modern science and technology are widely used in the whole process of cement dry process production to make cement production highly efficient. High-quality, resource-saving, clean production, environmental protection requirements and the large-scale process equipment, production control automation, the implementation of scientific management of modern cement production methods; among them, raw material ingredients and clinker calcination are the two core processes of the entire production process. Generally speaking, in the new dry process cement production technology, in order to ensure the stability of the calcination process, improve the clinker production and quality of the kiln, the raw material uniformity (stability) requirements and the control requirements of the content of each element are far more than other kiln The type must be more rigorous; a lot of practical experience also proves that only in this way can we fully display and reflect the advanced nature of the new dry process cement production technology.
Therefore, in the process design of the new dry cement production line, higher requirements have been put on the control indexes of various elements in the raw fuel:
1. Control the chemical composition of raw fuel to avoid the entry of harmful substances.
Since R2O (K2O+Na2O), SO3-2, and Cl2 in the raw meal will affect the clogging of the preheater precalciner system in the new dry process, after determining the type and mix ratio of the raw materials, It is necessary to verify whether the harmful components in the raw materials meet the requirements at all times. Otherwise, it is necessary to consider changing the raw materials or rate values, or adopt bypass bypass measures to reduce the circulating enrichment of alkali, sulfur, and chlorine to bring new dry kiln systems. The adverse effects.
(1) Magnesium Oxide (MgO)
When the clinker contains a small amount of MgO, it can reduce the firing temperature of the clinker, increase the amount of liquid phase, reduce the viscosity of the liquid phase, and facilitate the firing of the clinker; In the Portland cement, MgO and the main clinker minerals are combined The maximum content is 2% (by mass), and parts exceeding this amount are free in the clinker, resulting in volume expansion and cracking inside the solidified solid that has hardened.
(2) Free Silica (f-SiO2)
The vermiculite is a harmful impurity in the raw materials. The vermiculite has serious wear on the equipment and has adverse effects on the kiln grinding operation.
(3) Chlorine chloride mainly forms CaCl2 or chlorinated alkali in the calcining system. Its volatility is particularly high. Almost all of it is volatilized again in the kiln, and condensation occurs at the exit of the preheater, resulting in the accumulation of chlorine and alkali. The content of chloride in the raw material of the preheater is increased by nearly one hundred times, causing blockage of the preheater crust. For this reason, the universal control threshold for chlorine content in raw materials in the world is ≤0.015%.
(4) Alkali (K2O+Na2O)
The influence of alkali on the production of cement mainly has two aspects: one is to influence the normal production of the new dry clinker burning system; the second is to influence the quality of clinker. The burning of raw materials with high alkali content may easily cause clogging in the flue, precalciner, and preheater; the sintering temperature range in the rotary kiln is reduced, the thermal system is unstable, the sand is severe, and the kiln skin is loose. The life of the lining is shortened and the quality of the clinker is reduced. If it is severe, normal production will not be possible. If the clinker content is too high, the setting time will be shortened, resulting in sudden condensation, increasing the water content of the standard consistency of the cement, increasing the free calcium oxide in the clinker, poor stability, reduced flexural strength, and 1 day and 3 days. The compressive strength of the sky slightly increased, but the compressive strength of 7 days and 28 days decreased significantly.
(5) The sulfur-sulfur alkali ratio is an important control index of the cement calcining process. If the SO2 content is rich, it is often easy to cause clogging of the preheater crust or ringing in the kiln; otherwise, if the alkali content is rich, it will affect the normal operation of the preheater.
2. Control the fluctuation of various components of raw materials, strengthen analysis and ingredients of raw fuel, and strictly control the fluctuation range of various values.
Table 1 Quality Control Standards for Raw Materials of a Cement Plant (Relevant Chemical Composition Analysis)
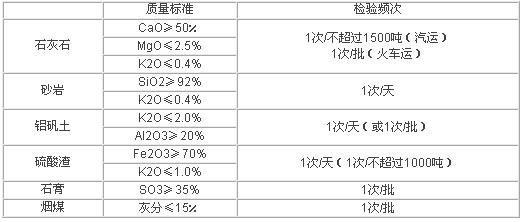
Table 2 New dry process quality control standards for a cement plant (chemical composition analysis related part)
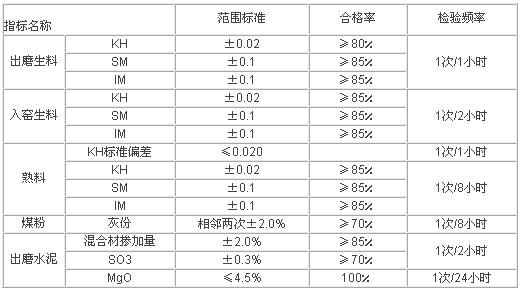
To sum up, in order to meet the requirements of the new dry process cement production conditions, all the chemical components of the raw fuel in the production process must be analyzed and controlled in a timely and accurate manner. The traditional chemical analysis methods can no longer meet the requirements of the production process. Need; At present, many new dry cement plants are equipped with corresponding multi-channel X fluorescence analyzers in order to achieve good quality control indicators. Due to the limitation of the analytical speed of chemical analysis methods, in fact, the use of chemical analysis methods only means the significance of post-event monitoring for the production process, and there is no control significance. It is often caused when we find that a certain control link has problems. As a consequence, it brought great losses to the factory.
Take the raw material batching process as an example: The full analysis of the raw meal by the chemical analysis method is generally one/8-hour (a few cement production enterprises use one/four hours, but the analysts have labor intensity, large numbers, and high costs) when ingredients When a problem arises, it usually takes time for the entire analysis to come out. It may be several hours before the problem arises. Even a 1,000-ton-per-day cement production line will have hundreds of tons of problems. Affecting the stability of the calcination process, especially for a production line using a continuous raw material homogenization library, the consequences of this situation are very serious. With the X Fluorescence Analyzer, we can provide accurate data for a full raw meal analysis every hour (and every half hour if needed) so that the target values ​​of ingredients, ingredients, and related The equipment is controlled, adjusted and monitored to ensure the stability of the raw materials in the kiln to ensure the stability and continuity of the calcination process.
The purpose of using the X-ray fluorescence analyzer is to make full use of the advantages of the X-ray fluorescence analyzer for rapid and accurate detection and tracking of all raw materials, raw materials, clinker, and cement in the whole process, and for different situations by the DCS system. Real-time adjustments enable real-world pre- and intra-event control; without the timely and accurate analysis of the elements in the material provided by the X-Fluorescence Analyzer, the DCS system will not be fully functional. Therefore, the real significance of using X-ray fluorescence analyzer is to reduce process accidents, stabilize quality, and increase production. At the same time, the use of X-ray fluorescence analyzer can also help to comprehensively strengthen and improve the overall management level of cement production companies, and can greatly reduce analysts. Preparation, saving chemical reagent costs.
Table 3 Application Example: Application of X-Fluorescence Analyzer in Beijing Cement Plant
Snack Shelves
Snack Shelves,Small Snack Shelves,Snack Shelves Shop,Snack Display Shelves
Jiangsu Jinyihao Metal Science And Technology Co., LTD , https://www.jyhshelf.com